Chemical Industry Meets Industry 4.0 and OEE Goals with Real-time Analytics to Increase Factory Performance
The chemical industry accounts for 12% of manufacturing in North America, transforming raw materials into chemical-based products. It serves many industries including automotive, agriculture, consumer goods, industrial operations, and transportation. Chemical sectors include pigments, food additives, synthetic rubber, polymers, resins, plastics, acids, and fertilizers.
The chemical industry faces many challenges including variations in the availability, quality, and cost of raw materials, meeting fluctuating demand for products in a global economy, and adhering to increasingly strict regulations. One of the biggest challenges in chemical manufacturing today is learning how to combine production and control system data in real-time to adjust formulas and processes as product flows through production.
Moving forward, chemical manufacturers need more efficient ways to monitor quality issues in real-time, particularly for the quality and performance of large reactors. Correcting flaws in the production process and predicting downtime of machines are critical factors for increasing efficiencies on the production floor.
The productivity of chemical manufacturers can be improved by smart manufacturing techniques such as predictive asset management which collects data from sensors on critical equipment so operators can identify patterns to predict and diagnose possible breakdowns. Advanced analytics from these techniques can substantially raise the level of understanding of what happens in a chemical plant’s manufacturing operations. Since energy costs contribute significantly to chemical manufacturing costs, predicting these potential breakdowns and preventing them can reduce energy waste.
To remain competitive, chemical manufacturers need to increase productivity and improve quality to meet customer’s specifications while reducing costs. Investing in digital transformation allows businesses to gain better control of processes and ensure clearer analytical insights to improve production decisions.
Digital Transformation for Chemical Manufacturing
In today’s competitive market, decision makers at all levels must be equipped with the best intelligence to make informed decisions at the right time. This process begins with collecting data from each machine on the plant floor and consolidating it into meaningful information for different levels of the organization. The goal is to deliver contextualized actionable information to plant floor managers and top-level executives in real-time. To do this, you need to implement digital technology that revolutionizes your factory through a series of adaptive changes.
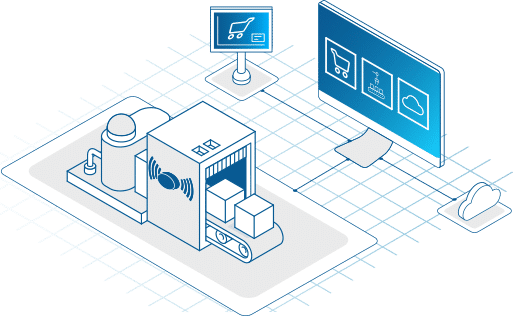
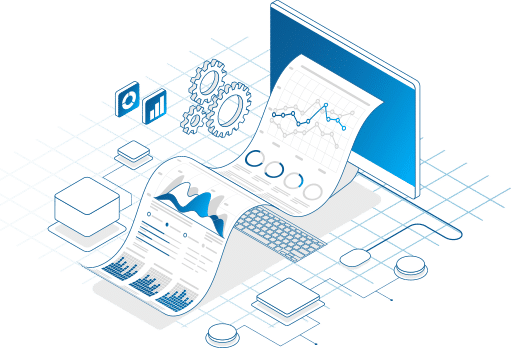
How FactoryEye Transforms Productivity for Chemical Manufacturers
FactoryEye is an affordable Industry 4.0 solution for mid-sized manufacturers that transforms data into actionable intelligence and provides visibility from the plant floor to the top floor. It monitors the entire process to enable chemical producers to achieve objectives such as:
- Improve machine learning and intelligence with a better connection of equipment and existing IT resources alongside smart data collection to improve sales, production, and agility.
- Digital recipe management and integration of electronic weights for adherence with product specification – at each stage, product is analyzed to compare inputs and outputs in real-time which ensures higher quality and reduces waste.
- Improve cost per unit by continuously monitoring, in real-time, equipment OEE so that teams increase outputs per work order with maintenance management to optimize product quality.
- Scrap reduction through the implementation of real-time statistical process control (SPC) to execute preventive activities based on trends and changes in product and production parameters.
- Seamless connectivity of key information systems like ERP, MES, PLM and QMS enables optimization of production planning, scheduling, procurement, and logistics.