Resilient structures and intelligent data management are key to remaining successful in these uncertain times of rising energy costs, raw material shortages, hard-to-calculate production capacity situations, fragile supply chains, the Ukraine war and the enormous shortage of skilled workers.
Intelligent data management includes a central data strategy, digitized processes, future-proof IT platforms, intelligent analysis tools (BI), and appropriate KPIs.
While badly needed digital individual projects were implemented during the Corona pandemic, many companies still lack an end-to-end digital business model. Intelligent data management that forms the basis for data-driven decisions is lacking. In addition, companies would be prudent, especially now, to continue driving digital transformation throughout their operations, automate processes and introduce missing tools.
We are heading towards a data-driven future with gigantic data volumes. According to IDC, the amount of real-time data will grow to about 30% by 2025, and more than half is currently not used further. Why? The reasons are complex: multiple data silos and autarkic applications, legacy systems, and manual processes at headquarters and branch offices. Addressing these issues is key to a proper data strategy.
Legacy Silos
Many legacy systems have been running for many years, such as ERP, MES, PLC, MED, QM, MM, PLM, SCM and CRM. They have grown over time without being aligned and synchronized. Deployed independently in individual business units or departments, they act largely independently of each other, pursue different goals, and form the basis of the well-known data silos.
More data silos due to individual digital projects
The projects prompted by Corona increased the level of digitization in numerous companies. Often, however, these were localized digitalization activities, where only certain core processes in a business unit were automated and digitalized. Due to the lack of an overall digital strategy, the flow of newly acquired data was frequently not thought out, and integrations were absent, unstructured or incomplete. This resulted in additional silos from business data in enterprise resource planning and customer information systems, to data from connected machines, devices and sensors from the production floor.
Legacy systems, new applications, and beyond the organization
Current digitalization involves the use of disruptive technologies and concepts. But, while increasing digitalization is essential, revolutions are normally not the optimal approach. Integrating legacy systems and new applications and improving business processes provides an assured path to full digitalization – with incremental improvements forming the basis of the strategy.
The goal must be to break down data silos and make data from all sources accessible, structured and evaluated. Implementation of this goal can be extended by connecting to suppliers and sales partners enabling a complete data flow and additional data transparency.
Big Data Value
Today, it is more important than ever for operations and manufacturing management to make fundamental decisions based on broad and reliable data and analysis. It’s not enough to collect and process data from a single business unit such as IoT machines and production equipment. It is necessary to draw on additional data from existing business applications in all business areas, such as warehouses and purchasing.
Central digitization and integration platform
Many digitalization solutions are focused on capturing data from a subset of the company’s IT systems – operations, production systems, logistics or financial systems. However, truly meaningful digital migration connects all aspects of the business. This is made possible with modern Industry 4.0 solutions. They enable companies to collect, process and analyze all data quickly and completely. No matter where they are located within the organization or the supply chain.
Data hub and BI as a basis
Some of these Industry 4.0 solutions already include a data lake and analysis tools (BI). They form a sound basis for intelligent data management across application and organizational boundaries. Information such as customer master data can be linked with market and competitive data. Machine and production floor data can be linked to quality and after-sales service data and retrieved in real time.
Sound data evaluations, such as financial reports, can be presented clearly in visual dashboards and accessed at any time, and from any location. Decision makers can analyze relevant and clearly defined KPIs and improve OEE.
In addition, essential workflows are optimized and automated. Expenditure and time spent on tasks can be reduced and more effective inventory management and forward planning can be achieved, and machine repairs are simplified.
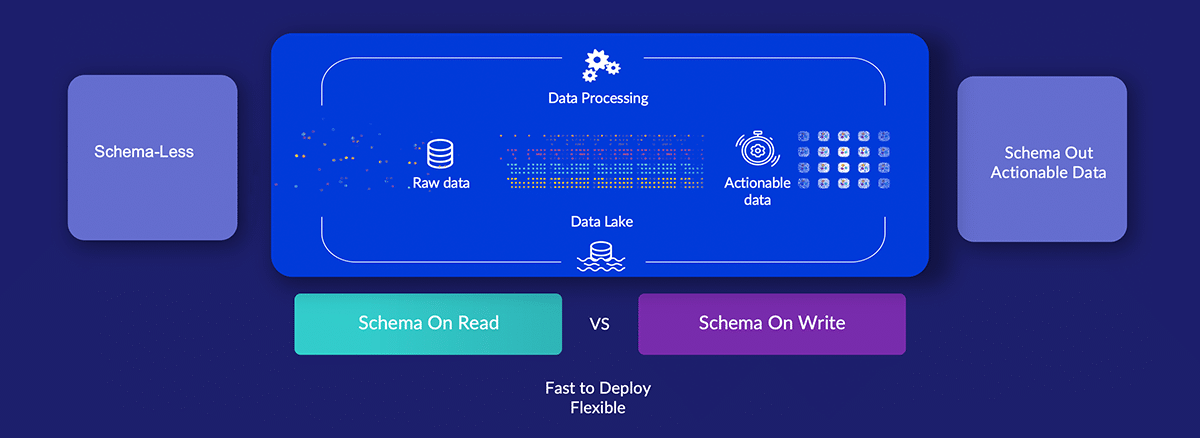
Data lake benefits
Key points to bear in mind about intelligent data management:
- Future-oriented data management includes a suitable organizational structure, tailored operating models for Big Data and Data Analytics, and Industry 4.0 solutions.
- An efficient data strategy is in place when business-relevant data from all sources can be collected, processed, analyzed easily, and shared efficiently in one platform.
- Flexible digitalization and integration platforms support data-driven decision-making.
- With access to accurate real-time data and insights across the supply chain, managers can make the right decisions in a timely manner.
About FactoryEye
FactoryEye is an advanced Industry 4.0 manufacturing & cross-organizational intelligence platform for full visibility and actionable data insights. FactoryEye enables manufacturing personnel at all levels to make data-based decisions and the manufacturing organization as a whole to achieve business excellence. Contact us to see how we can help you drive operational and business excellence.