Meeting Industry 4.0 and OEE Goals with Real-time Analytics to Increase Factory Performance in the Automotive Parts Industry
The automotive parts manufacturing industry is constantly adapting to a wide variety of variables including fluctuations in availability and pricing of raw materials, fluctuations in demand for parts, the rise of global competition and the need for continuous improvement on the shop floor.
As the automotive industry adapts to a future with electric drivetrains, autonomous technology, connectivity, and mobility options outside traditional car ownership, auto parts vendors must evolve to meet these new challenges.
In addition, auto parts manufacturers are seeing significant downward pressure on pricing from their automaker customers, while regulations and quality requirements become stricter. These are forcing businesses to get creative in the search for ways to reduce costs and increase productivity and efficiency.
Digital Transformation in the Auto Parts Industry
In today’s competitive market, decision makers at all levels must be equipped with the best intelligence to make the right decisions at the right time. This process begins with collecting data from each machine on the shop floor and consolidating it into meaningful information for different levels of the organization. The goal is to deliver contextualized actionable information to shop floor managers and top-level executives in real-time. To do this, you need to implement digital technology that revolutionizes your factory through a series of adaptive changes.
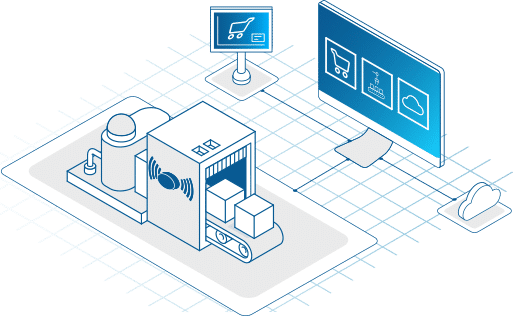
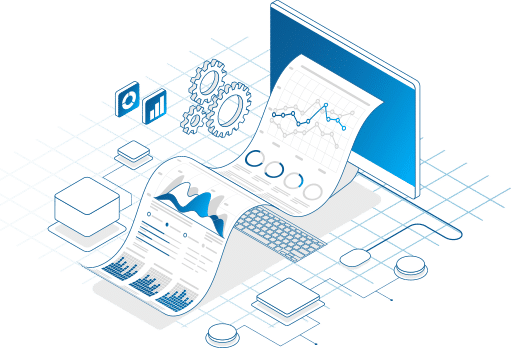
How FactoryEye Transforms Productivity in the Auto Parts Industry
FactoryEye is an affordable Industry 4.0 solution for mid-sized domestic manufacturers that transforms data into actionable intelligence and provides visibility from the shop floor to the top floor. It supports monitoring of the entire process to enable auto parts manufacturers to achieve objectives such as:
- Sensors installed in key production, assembly, packaging machines, workstations, and transport systems provide enormous amounts of actionable data that pinpoints bottlenecks, unscheduled disruptions, or equipment that needs servicing before these problems become acute.
- Centralizing the data of all production locations, subcontractors, DCs and suppliers in the cloud allow collecting data directly from the equipment, rationalizing it using intelligent analytics, and using the results to develop an agile, real-time assessment of ways to improve delivery times and costs.
- Inline process control, results of incoming material lab tests, and smart quality management improve quality and reduce risks of recalls.
- Seamless connectivity of key information systems like ERP, MES, PLM and QMS enables optimization of production planning, scheduling, procurement, and logistics.